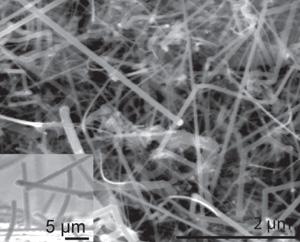
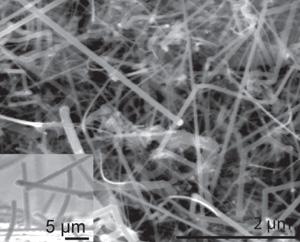
Portable Power Grows Potent
Seventeen years after they were first commercialized, lithium-ion batteries are the fastest-growing type. But as processors in computers and other electronic devices get faster, the demand for power keeps growing.
Seventeen years after they were first commercialized, lithium-ion batteries are the fastest-growing type. But as processors in computers and other electronic devices get faster, the demand for power keeps growing.
A team of researchers at Hitachi High Technologies America, Lawrence Berkeley National Lab, and Stanford University is developing an alternative material that could double the capacity of lithium-ion batteries. If the material—known as silicon nanowires—proves itself in the lab and can be commercialized, theoretically it could be scaled for use with any size battery, from AAAs up to those powering electric cars.
The research bears watching by AV professionals because longer lasting portable power could create new flexibility.
Silicon nanowires remain relatively stable after being packed with and then drained of lithium ions during a battery’s charge-discharge process. The stability makes them an attractive option for boosting the capacity of rechargeable batteries. These images, both at the same magnification, show pristine silicon nanowires before (left) and after (right) the electrochemical cycling.
For example, out-of-home advertising is a growth market, but some places that are ideal for digital signage don’t have nearby electrical service. And the cost of running electrical cable to a display or projector can be steep—$100 or more, depending on factors such as distance, difficulty, conduit materials, and whether the new line pushes the building’s electrical infrastructure to the point that something has to be upgraded, such as a breaker panel.
In applications where those costs add way up, a portable power source, such as next-gen batteries, could be attractive. Granted, even next-gen batteries probably wouldn’t be a viable way to power an LCD display that consumes, say, 250 watts. But they could be viable for “electronic paper” displays, which use power only to change an image, not to maintain it.
Described in a December 2007 Nature Nanotechnology article, “High-Performance Lithium Battery Anodes Using Silicon Nanowires,” the research is still in an early stage. But that nascence didn’t stop mainstream media such as Popular Mechanics from trumpeting it as capable of boosting battery life by up to a factor of 10—though that’s highly unlikely.
“It’s probably not 10 times,” says Yi Cui, one of the researchers and an assistant professor in the Department of Materials Science and Engineering at Stanford University. “It’s very hard to get 10 times.”
So just how much of a boost might silicon nano-wires provide when they’re ready for commercialization? Probably about double, Yi says. “Look at battery history. Doubling capacity is a big deal.”
THINKING SMALL
All batteries have two electrodes: an anode (negative) and a cathode (positive). Yi and the other researchers currently are focused on the anode, which in today’s lithium-ion batteries is typically made of graphite. Silicon is an attractive alternative to graphite because it has 10 times more charge capacity. For years, other researchers have studied lithium silicide compounds for use in batteries because this material allows the silicon to store more lithium.
The big catch is that silicon swells 400 percent as lithium is inserted and extracted to produce electrical power. That swelling fragments the anode, permanently damaging it to the point that it’s nearly useless. “When something breaks, you lose capacity,” Yi says.
Yi and the other researchers are using silicon in the form of nanowires, each 100 nanometers wide. That’s about one ten-millionth of an inch, a size that mitigates the fragmentation problem. “They’re already smaller than the smallest piece you can break,” Yi says. “They’re not going to break any more.”
The researchers then pushed lithium into the silicon nanostructure to see if it would hold when used as a battery anode. “They don’t break, so we solved that problem,” Yi says.
So far, the researchers have put the silicon nanowire anodes through less than 100 cycles of inserting and extracting lithium, which is the process of charging and discharging the battery. More tests are required to see if the anodes hold up though more cycles—the amount that a battery goes through in a typical life span. “They look pretty good so far,” Yi says.
To boost a lithium-ion battery’s energy storage capacity even further, the anode improvement has to be complemented by a better cathode. “Getting up to 10 times [capacity] is a lot harder to do because you’re limited by cathode materials,” Yi says.
Yi and the other researchers also are looking for ways to improve cathodes, but they can’t simply apply the silicon nanowire technology. That’s because anodes and cathodes are fundamentally different in terms of the roles they play in creating the flow of current that produces power.
“Anode requires the potential [the electrical equivalent of water pressure] to be low, and cathode should be high,” Yi says. “So they should be different materials.”
FUEL CELLS: READY FOR PRIME TIME?
Next-gen batteries aren’t the only technologies in development to meet the growing demand for longer-lasting portable power. Another example is fuel cells, which convert a mix of fuels and oxidants—such as hydrogen and oxygen, respectively—into electrical power.
The conversion occurs through chemical reactions, so in that sense, fuel cells are like batteries, except that they generate much more power and require periodic refueling.
Fuels cells could eventually provide an alternative to batteries. Here’s a typical Proton Exchange Membrane (PEM) fuel cell, which uses hydrogen for fuel and has a membrane (PEM) that allows hydrogen protons (H+) to transfer from anode to cathode. Each membrane cell is connected to an electric circuit. Hydrogen breaks into electrons and protons at the anode and electrons pass through the circuit to provide power. Electrons and protons then combine with oxygen at the cathode to produce water.”/>
Fuels cells could eventually provide an alternative to batteries. Here’s a typical Proton Exchange Membrane (PEM) fuel cell, which uses hydrogen for fuel and has a membrane (PEM) that allows hydrogen protons (H+) to transfer from anode to cathode. Each membrane cell is connected to an electric circuit. Hydrogen breaks into electrons and protons at the anode and electrons pass through the circuit to provide power. Electrons and protons then combine with oxygen at the cathode to produce water.
For example, two years ago, UltraCell, a Livermore, Calif.–based company, announced a 2.2-pound prototype fuel cell capable of powering a laptop computer for 14 hours.
That application is noteworthy for a couple of reasons: Consumer products ship in much higher volumes than pro gear, so the more fuel cells are sold, the more the price of the technology drops. More sales also means more revenue that fuel cell manufacturers can plow into R&D to extend the life and power to the point that they become practical for use in pro AV products.
Over the past decade, researchers have made major advances in fuel cells, including increasing their life span and the amount of power they generate. They’ve also reduced costs by using less expensive carbon materials instead of pricey platinum.
Even so, fuel cells are still a niche play in the sense that it’s difficult to find a consumer or professional electronic device with one inside. Large fuel cells capable of powering, say, a house have been commercially available for years, but scaling the technology down has proved more challenging than expected. For example, in 2002 and 2003, some laptop and cell phone vendors had said they expected to start shipping fuel cell-powered products by 2007. That didn’t happen, but it doesn’t indicate insurmountable hurdles.
By comparison, batteries are a mature, widely used technology. Although Yi and his colleagues are using materials that are significantly different than what are found in today’s batteries, their technology still has incumbency on its side in the sense that it’s easier to commercialize. That’s because battery manufacturers understand batteries and how to make them, whereas fuel cells are fundamentally different and thus require new manufacturing equipment and processes. “Battery is a lot more practical at this moment,” Yi says.
But there is at least one more significant caveat. The technology described in the Nature Nanotechnology article uses processes that battery manufacturers can’t simply drop into their existing manufacturing lines. That’s a hurdle in terms of convincing battery vendors to adopt their technology, which is why the researchers also are working on another process that Yi says is compatible with existing battery manufacturing processes.
The result is a horse race, with time-to-market, power, longevity, and manufacturing costs among the factors that will determine whether fuel cells or silicon nanowire batteries emerge as the favorite among manufacturers. Although it will take years of testing and refinement before silicon nanowire technology is ready for commercialization, Yi is optimistic.
“There’s no road block we see that we can’t overcome. We’re using a process that’s well understood and widely used in the semiconductor industry. Five years would be a reasonable estimate.” Where silicon nanowire lithium-ion batteries will debut is anyone’s guess at this point. In theory, the technology could be used in everything from MP3 players to electric cars. But Yi isn’t making any predictions about the initial applications. “I might prove myself wrong five years later.”
Tim Kridel is a freelance writer and analyst who covers telecom and technology based in Columbia, Mo. He can be reached at [email protected].